Безопасность на звук


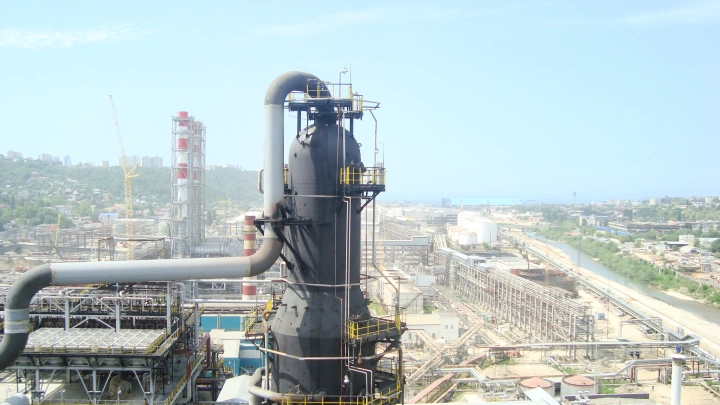
В России создано единственное в мире эффективное решение определения в режиме реального времени дефектов на объектах ТЭК с помощью метода акустической эмиссии
Текст: Павел Трофимук
Цифровая диагностика
Когда в сфере промышленной безопасности ТЭК говорят о системах дистанционного контроля, в первую очередь подразумевают передачу данных с технологических датчиков и их последующую наукоемкую обработку оператором. Уже в таком подходе заложен огромный риск: получаемые данные отображают сведения о конкретном производственном этапе, условно температуру и давление. И если они соответствуют технологическому процессу, то оператором предполагается, что все в норме. Но здесь не учитывается главный фактор: физическое состояние устройств, сооружений и зданий, где эти процессы проходят, и субъективная оценка происходящего человеком.
Акустическая эмиссия (АЭ) — эффективный метод неразрушающего контроля, основанный на явлении возникновения и распространения упругих колебаний (акустических волн) в различных процессах, например, при деформации напряженного материала (внутренней локальной динамической перестройки его структуры), истечении газов, жидкостей и др. Проще говоря, любой материал издает звук характерный для его сиюминутного состояния. По этим звуковым волнам можно предугадать критическое развитие процессов разрушения материала. Физические принципы такого метода известны давно, но сам метод долгое время считался несовершеннным: на реальных производствах слишком шумно, чтобы «услышать» нужный звук. Сегодня эта проблема успешно решается компанией «Диаформ»: распознавание нужных волн происходит в режиме реального времени посредством алгоритмов глубокой цифровой фильтрации сигналов АЭ, а также последующей работы математического алгоритма системы принятия решения и техническом состоянии устройства или изделия. Главная задача, стоящая перед разработчиками, – исключение человеческого фактора в процессе диагностики.
Принципиальная схема построения системы акустико-эмиссионного контроля выглядит довольно очевидной. Сигнал с множества датчиков, закрепленных на контролируемом объекте (а это может быть резервуар, трубопровод и т.д.) поступает в шкаф сбора и оцифровки данных. Количество шкафов зависит от количества подключаемых датчиков и конфигурации системы. Кроме датчиков АЭ также могут быть интегрированы в систему любые типы других датчиков, в том числе угла наклона, деформации, осадки грунта, акселерометры, гидроуровни и т.д. Показания датчиков по каналам связи передаются на сервер. Каналы связи могут быть проводные и беспроводные, включая GSM и Wi-Fi. На сервере происходит процедура цифровой обработки данных, и результат поступает к диспетчеру. Кроме того, итоговая информация о техническом состоянии объекта дублируется на любые устройства заинтересованных лиц. Всего к системе может быть подключено несколько сотен удаленных пользователей.
Запатентованная технология автоматически распознает дефекты
На сегодняшний день автоматизированная цифровая обработка данных является современным мировым трендом, но говорить о массовом внедрении подобных решений в сфере неразрушающего контроля и технического диагностирования пока не приходится. Необходимо не просто «услышать» звук среди множества подобных, но и распознать в этом звуке важную информацию о дефекте, о его развитии и росте.
Оригинальное решение разработчиков компании «Диаформа» позволяет уже сегодня в условиях реального производства на текущих рабочих параметрах оборудования автоматически обнаруживать и выделять на фоне помех полезный сигнал от источника разрушения. Трудились над этим проектом более 15 лет. Каждый этап реализации решал вновь выявленные в ходе многочисленных экспериментов проблемы. Работы проводились как в лабораторных, так и в полевых условиях – на реальных действующих объектах.
В результате была создана система мониторинга нового поколения, не имеющая аналогов в мире, работа которой исключает принятие решения, основанного на субъективной человеческой оценке.
Запатентованная технология беспороговой регистрации данных (БРД) позволяет автоматически распознавать дефекты. Технология БРД без участия оператора обеспечивает оценку технического состояния объекта контроля на фоне случайных индустриальных помех.
Система на ранней стадии выявляет зарождающиеся и развивающиеся трещины, в том числе коррозионное растрескивание под напряжением, дефекты электрохимической коррозии, опасные механические повреждения, зоны пластической деформации, потерю устойчивости и герметичности.
Программный модуль акустико-эмиссионного контроля состоит из трех блоков.
Первый – блок цифровой фильтрации. Многокаскадная цифровая фильтрация позволяет обнаружить и выделить полезный акустико-эмиссионный сигнал на фоне шумов.
Второй – блок определения диагностических признаков. В ходе обработки производится расчет локальных статистических параметров сигналов АЭ, описывающих процессы возникновения и развития опасных дефектов.
Третий блок – система принятия решений. Это отдельная интеллектуальная система, основанная на принципах машинного обучения, позволяющая распознавать и классифицировать дефекты, развивающиеся в объекте контроля. Данный блок позволяет в автоматическом режиме распознавать развитие дефектов, классифицировать их по степени опасности и, как результат, на выходе сформировать соответствующее информационное сообщение. Блок является помехоустойчивым, т.е. результат принятия решения слабо зависит от влияния случайных шумов и помех различной природы (механические удары, импульсные электромагнитные помехи, технологические шумы, атмосферные явления и т.д.).
В итоге система классифицирует дефекты по трем степеням опасности:
- опасные развивающиеся дефекты не зарегистрированы (эволюционные процессы отсутствуют) – внимание не требуется;
- обнаружены опасные развивающиеся дефекты – требуется внимание;
- обнаружены критически опасные развивающиеся дефекты – требуется принятие мер по устранению дефектов.
Успешная апробация на промышленных объектах
Технология БРД была уже успешно применена на ряде объектов, где продемонстрировала высокую эффективность в условиях особо опасных производств. С ее помощью был произведен контроль осевых сильфонных компенсаторов, установленных на трубопроводе перегретого водяного пара установки дегидрирования и ректификации стирола на ЗАО «Сибурхимпром» в Перми; проведена диагностика дефектных участков, магистрального нефтепровода Демьянское – Конда АО «Транснефть-Сибирь», осуществлен комплекс работ по контролю реакторов высокого давления ООО «Томскнефтехим» (ПАО «СИБУР») и прочее. Всего более полутора десятков успешно выполненных работ на опасных производственных объектах.
Сейчас система диагностического мониторинга, основанная на технологии беспороговой регистрации данных для акустико-эмиссионного контроля и мониторинга технического состояния шаровых резервуаров хранения жидких этана и этилена, устанавливается на предприятии ООО «Иркутский завод полимеров».
Говоря же, как принято это делать, об экономическом эффекте внедрения этого решения, достаточно вспомнить штраф Росприроднадзора – 146,2 млрд рублей, которые выплатил «Норникель» за разлив соляры в результате разгерметизации резервуара на Таймыре в мае 2020 года.
Был ли вам полезен данный материал?

Подписывайтесь на канал ru-bezh.ru
в Яндекс.Дзен