Проблемы дистанционного мониторинга, контроля и надзора за эксплуатацией объектов в ТЭК и промышленности


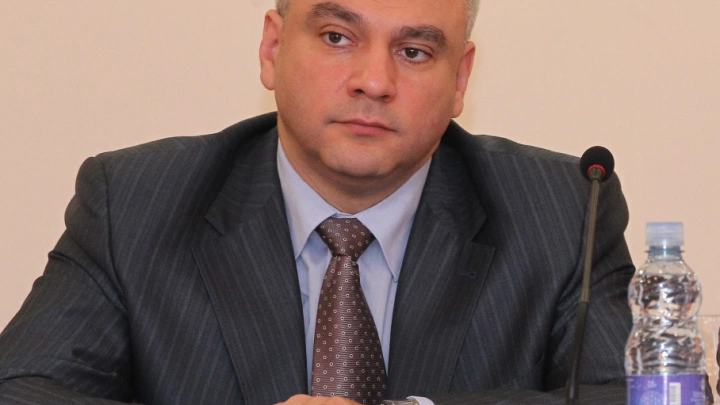
Борис Харас
Генеральный директор ООО «ИнфТех»
Постановление Правительства РФ № 2415 от 31.12.2020 г. «О проведении эксперимента по внедрению системы дистанционного контроля промышленной безопасности» установило проведение с 1 февраля 2021 года по 31 декабря 2022 года эксперимента по внедрению системы удаленного мониторинга опасных промышленных объектов. Тестирование удаленного контроля промышленной безопасности возложено на компанию «Сибантрацит». Но независимо от итогов эксперимента, которые пока не обнародованы, внедрение систем удаленного мониторинга, контроля и надзора на опасных производственных объектах (ОПО) в России до сих пор происходит фрагментарно либо с ограниченным функционалом. В чем причина?
Попытки внедрения
Эксперимент по дистанционному мониторингу ОПО, запущенный правительством Михаила Мишустина в канун 2021 года, стал второй попыткой государства перевести надзор за промышленной безопасностью на рельсы цифровизации. До этого в 2019 году тогдашний глава Ростехнадзора Алексей Алешин в рамках цифровой трансформации надзорной деятельности анонсировал внедрение систем дистанционного контроля в рамках реализации реформы контрольно-надзорной деятельности анонсировал запуск аналогичного пилотного проекта на базе предприятий ПАО «СИБУР Холдинг». Для дистанционного мониторинга должны были стать доступны системы противопожарной защиты, связи и оповещения персонала, позиционирования персонала на объекте, а также система контроля технологических параметров работы оборудования и аварийных остановок.
Однако, если судить по отсутствию сообщений об итогах пилотных проектов, текущие инструменты контроля технического состояния промышленных объектов по-прежнему опираются на «бумажные технологии» с минимальным использованием средств измерений и объективного контроля со стороны надзорных органов. Что не удивительно. Любая система контроля и надзора может базироваться исключительно на развитой системе промышленной автоматизации и на внедренной владельцем актива системе удаленного мониторинга и диагностики.
Для этого необходимо соблюдение нескольких факторов.
Базовый уровень автоматизации производства
Владельцы активов за последние 10 лет инвестировали существенные средства во внедрение средств измерений и в Автоматизированные системы управления технологическими процессами (АСУ ТП). Тем не менее системы удаленного мониторинга и диагностики по-прежнему внедрены на очень ограниченном числе предприятий.
Разница заключается в том, что АСУ ТП и системы противоаварийной защиты (ПАЗ) обеспечивают автоматическую защиту быстро развивающихся процессов в случае выхода параметров за допустимые границы. При этом медленно развивающиеся процессы деградации технического состояния промышленного оборудования и объектов в целом остаются за рамками АСУТП и систем ПАЗ. Например, в случае коррозии, изменения геометрии фундамента самого объекта средства измерений не используются. Контроль за состоянием оборудования, подверженного такого класса деградациям, требует внедрения специальных средств измерений и создания специализированных аналитических систем.
Наличие цифровых двойников и актуализация данных
Проблемой для большинства компаний при работе с цифровыми двойниками является актуализация данных. Любой промышленный объект подвержен ремонтам и модернизациям. В случае когда это находит отражение в информационных системах, на актуализацию данных могут уходить недели, иногда, месяцы. Культура производства и общий уровень информатизации и автоматизации зачастую негативно влияют на процесс актуализации данных в информационных системах. Это приводит к резкому снижению эффективности процессов удаленного мониторинга и диагностики оборудования.
Модернизированные системы управления жизненным циклом активов
Основными фазами жизненного цикла (ЖЦ) для производственных активах являются Проектирование, Строительство, Эксплуатация, Ликвидация. Автоматизация бизнес-процессов на каждом этапе ЖЦ осуществляется с помощью специализированных информационных систем.
На первом этапе используются системы автоматизированного проектирования – САПР (CAD, CAM, CAE), на втором – системы управления информационными моделями объектов и активов класса BIM, на третьем – системы управления производственными процессами класса MES. Интеграционной «шиной», связывающий информационные системы на всех этапах, является система управления инженерными данными (СУИД). Инструментов ведения единой сквозной информационной модели актива в России на сегодня не существует.
На фоне отсутствия отечественных информационных технологий рядом крупных компаний приобретены зарубежные СУИД-решения (в частности, технологии Aveva Engineering), но эффективность их внедрения на фоне санкций вызывает сомнение.
Отсутствие развитой СУИД и единой информационной модели актива на всех этапах его жизненного цикла (единого цифрового двойника объекта) приводит к тому, что все инструменты анализа технического состояния актива, основанные на данных измерений и объективного контроля, существуют в разных информационных системах, при этом имеются сложности в их совместной интерпретации и в сопоставимости. Например, компания Bimeister предлагает свое решение по СУИД, но не предлагает интегрированных решений по Системам управления техническим обслуживанием и ремонтом (ТОиР), САПР и BIM. Ведущим игроком на рынке САПР является компания АСКОН, но и у нее полностью интегрированного решения с ТОиР нет. Также у данных вендоров не представлены в продуктах предиктивные жизненные циклы (известные как полностью управляемые планом) – вид жизненного цикла проекта, при котором содержание проекта, а также сроки и стоимость, необходимые для выполнения данного содержания, определяются на как можно более ранней стадии жизненного цикла.
Эффективность эксплуатации производственных активов
Согласно данным компании GMCS (российский IT-интегратор), доля операционных затрат на ТОиР может достигать 25-30% в себестоимости добычи нефти и газа, а доля операционных затрат на обслуживание горнодобывающих предприятий доходит до 30-50%. Такие существенные операционные затраты отвлекают финансовые ресурсы предприятий от задач модернизации и повышения промышленной и экологической безопасности.
Сегодня большинство промышленных предприятий использует реактивный и планово-предупредительный метод обслуживания (ППР), что не позволяет повысить эксплуатационную эффективность и сократить затраты. Так, при реактивном методе (наработка оборудования на отказ с последующим ремонтом), который применяется для некритичного оборудования, существенно увеличиваются затраты на восстановление и значительны простои. При планово-предупредительном методе (обслуживание через фиксированные интервалы времени/наработки, определяемые производителем) не учитывается реальное техническое состояние объекта и есть вероятность повышенных затрат на ТОиР для малонагруженного оборудования.
Современные информационные системы позволяют выявлять аномалии в работе оборудования на ранней стадии, прогнозировать остаточный ресурс до вероятного функционального отказа, что дает возможность выявлять проблемы на ранней стадии и выполнять ТОиР на основе фактического состояния и с учетом рисков. Внедренные такие системы в совокупности с методикой обслуживания оборудования по фактическому состоянию позволяют уменьшить количество поломок оборудования в среднем на 30-35%, сократить расходы на его обслуживание на 10-20% [2], уменьшить время простоя в диапазоне от 30 до 50% [3], а также снизить объемы реактивного (внепланового) обслуживания на 10-44% [4].
Однако в настоящее время данный подход применяется на практике недостаточно широко. Ключевых барьеров несколько.
Во-первых, культура производства. Для подавляющего большинства промышленных предприятий проще соблюдать планово-предупредительный подход в рамках регламентов производителей и инструкций Ростехнадзора, чем переходить на управление по состоянию оборудования.
Во-вторых, переход на управление активами по состоянию требует не только современных измерительных приборов и информационных систем обработки больших данных, но внедрения новых для владельцев активов бизнес-процессов постоянного мониторинга и диагностики состояния активов, т. е. привлечения специалистов иных квалификаций, в частности инженеров по надежности.
В-третьих, имеются очевидные барьеры на стороне контролирующих и надзорных органов, которые привыкли работать в парадигме ППР, хотя на сегодня имеется нормативная база, разрешающая вести управление эксплуатацией активов по состоянию оборудования. Свыше 10 лет назад АО «Рязанская нефтеперерабатывающая компания» одной из первых в РФ начала перестраивать систему управления на управление по состоянию оборудования. До сих пор этот опыт остается единичным.
Координация акторов, осуществляющих мониторинг и контроль за эксплуатацией промышленных объектов
К основным акторам, занимающимся процессами контроля за техническим состоянием промышленных объектов, следует отнести владельца актива, эксплуатанта актива (если отличается от владельца), надзорный орган (Ростехнадзор). Если объект специального назначения, то появляются специализированный отраслевой надзорный орган, Росимущество, Минэнерго РФ или иное отраслевое министерство, МЧС.
Ответственным за эксплуатацию актива является его владелец. Именно владелец актива устанавливает средства измерений, АСУ ТП, системы удаленного мониторинга и диагностики технического состояния. Все остальные акторы в соответствии с утвержденными регламентами на основании данных, получаемых от владельца актива в режиме офлайн, осуществляют функции контроля и надзора.
Данное распределение функций приводит к следующему.
- Владелец актива фильтрует данные, передаваемые в надзорный или контролирующий орган, доступ к данным измерений технических параметров объекта в режиме онлайн отсутствует.
- Отсутствует единая информационная модель актива на стороне контролирующего и надзорного органов, контроль строится на основе отчетов, возможность удаленной диагностики отсутствует.
- Контролирующий и надзорный органы никогда не имеют актуальной информационной модели (актуального цифрового двойника) актива. Все действия с активом, ремонты, модернизации в лучшем случае отражаются в информационных системах владельца.
- Контролирующие и надзорные органы не имеют современных информационных систем удаленного мониторинга, диагностики и предиктивного анализа, бюджет на внедрение таких систем не выделяется. Такого класса системы имеются в лучшем случае у владельца актива.
В итоге у контролирующих и надзорных органов отсутствуют как данные измерений в режиме онлайн, так средства для их обработки. Иными словами, все контролирующие органы сегодня полагаются исключительно на данные и результаты их обработки, получаемые от владельца актива. С учетом отсутствия в большинстве случаев современных средств измерений, объективного контроля, систем обработки данных удаленного мониторинга и диагностики все акторы оказываются в ситуации ограниченных возможностей инструментального контроля работы промышленных объектов. Безусловно, эффективность исполнения своих контрольных и надзорных функций сильно снижается.
Архитектура систем удаленного мониторинга и диагностики промышленного оборудования
Удаленный мониторинг и качественная диагностика производственного оборудования при помощи цифровых технологий требуют решения следующих задач:
- определения ключевых конструктивных, эксплуатационных и технико-экономических параметров оборудования на каждом из этапов его жизненного цикла;
- оснащения оборудования средствами КИПиА для фиксации необходимых параметров в автоматическом режиме;
- организация передачи данных телеметрии/параметров в режиме, близком к реальному времени;
- обеспечение хранения и доступности данных параметров для обработки и анализа;
- выполнение диагностических и прогнозных расчетов для раннего выявления аномалий в работе оборудования;
- визуализация первичных и расчетных данных, их анализ и моделирование механизмов диагностики и поведения объекта при различных условиях.
Если говорить об архитектуре современной информационной системы для решения указанных выше задач удаленного мониторинга, диагностики и прогнозирования технического состояния производственных активов, то ключевым элементом такой системы является информационная модель объекта («цифровой двойник»), которая позволяет описать оборудование и его параметры, накапливать исторические данные по этому объекту, описывать поведение объекта на всех этапах жизненного цикла – от проектирования до его ликвидации.
Рисунок 1. Концептуальная архитектура цифрового решения для удаленного мониторинга, диагностики и прогнозирования технического состояния производственного оборудования.
Неотъемлемыми элементами современной системы удаленного мониторинга являются развитые алгоритмы диагностирования и прогнозирования. Используемый в диагностике математический аппарат и методы машинного обучения обеспечивают выявление аномалий (потенциального отказа) на ранней стадии развития дефекта и точный прогноз остаточного ресурса до функционального отказа.
Сотрудничество владельцев активов и надзорных органов
Контролирующие и надзорные органы по роду своей деятельности обладают информацией о большом числе аварий, аварийных ситуаций. Это дает возможность построения современных экспертных баз, которые могут использоваться как в системах надзорных органов, так и в системах удаленного мониторинга и диагностики владельцев активов. На основе таких экспертных баз владелец актива или эксплуатант могут в автоматическом режиме с высокой степенью достоверности определять причины тех или иных результатов диагностики. Работа по созданию экспертных баз знаний может осуществляться надзорными органами и на коммерческой основе. Ключевым элементом при этом является качество экспертизы, возможность аналитики большого объема исторических данных по работе объектов.
7 шагов к внедрению дистанционного мониторинга
Среди ключевых условий внедрения дистанционного мониторинга в сфере промышленных объектов и опасных производственных объектов в России можно выделить следующие. Степень их реализованности и будет определять повышение надежности эксплуатации промышленных объектов.
- Повышение культуры управления производством
- Внедрение современных систем удаленного мониторинга и диагностики работы оборудования на основе детальных цифровых двойников объектов и процессов их эксплуатации. Оптимальным является внедрение систем предиктивной аналитики.
- Подключение к «цифровым двойникам», находящимся на стороне владельцев активов, всех контролирующих и надзорных органов с автоматическим получением отчетности на основе данных измерений параметров работы оборудования (получаемых и в автоматическом режиме, и на основе данных объективного контроля).
- Внедрение современных систем анализа данных на стороне контролирующих и надзорных органов.
- Создание экспертных баз знаний при активном участии экспертов контролирующих и надзорных органов.
- Развитие института DATA-аналитиков по работе с промышленным оборудованием.
Создание специализированных подразделений на стороне владельцев активов, занимающихся процессами управления надежностью работы оборудования.
Литература
- Что мешает современным компаниям повысить качество процессов ТОиР. [Электронный ресурс]. – URL: https://www.gmcs.ru/press-center/press-about/chto-meshaet-sovremennym-kompaniyam-povysit-kachestvo-protsessov-toir/. (дата обращения 04.09.2023 г.)
- Прогнозная аналитика – способ адаптации в новых экономических реалиях [Электронный ресурс]. – URL: http://www.iksmedia.ru/articles/5292204-Prognoznaya-analitika-sposob-adapta.html (дата обращения 01.09.2023).
- Использование расширенной аналитики для повышения производительности и прибыльности химического производств [Электронный ресурс]. – URL: https://www.mckinsey.com/industries/chemicals/our-insights/using-advanced-analytics-to-boost-productivity-and-profitability-in-chemical-manufacturing (дата обращения 01.09.2023).
- Глобальный прогноз рынка технического обслуживания на 2019-2027 гг.[Электронный ресурс]. – URL:https://www.inkwoodresearch.com/reports/global-predictive-maintenance-market/ (дата обращения 01.09.2023).
- Ранняя диагностика и прогнозирование надежности промышленного оборудования на основе «цифрового двойника». Жиляков С.А., Карасев Е.М., Левочкин С.Б, Плешивцева Т.А [Электронный ресурс – журнал «Neftegaz.RU» (№5, Май 2021)]. – URL: https://magazine.neftegaz.ru/articles/tsifrovizatsiya/682121-rannyaya-diagnostika-i-prognozirovanie-nadezhnosti-promyshlennogo-oborudovaniya-na-osnove-tsifrovogo/ (дата обращения 01.09.2023)
- Применение нейронных сетей для диагностики и прогнозирования технического состояния оборудования. Мустафина С.И., Жиляков С.А..Журнал «Автоматизация и информатизация ТЭК» 7(600).2023, ISSN604X
ООО «ИнфТех» является разработчиком российской системы удаленного мониторинга, диагностики и предиктивной аналитики промышленного оборудования iPredicta. Полностью отечественное решение построено на концепции «Индустрия 4.0» и технологиях промышленного интернета вещей (IIoT), что обеспечивает возможность создания и ведения информационной модели («цифрового двойника») производственного объекта, удаленный сбор данных параметров оборудования и их историческое хранение.
Подсистема диагностирования содержит ряд реализованных алгоритмов, которые используют зарекомендовавшие своей чувствительностью методы статистического анализа: метод многомерной оценки состояния (MSET) и последовательный тест отношения вероятностей (SPRT), корреляционный анализ.
Отдельное место в iPredicta занимает подсистема диагностирования и прогнозирования на основе нейронных сетей, которая позволяет решать задачи как классификации, так и регрессии при помощи различных методов. Это дает возможность использования нейросетевых технологий в задачах диагностирования и прогнозирования в различных производственных условиях.
iPredicta реализует функции оповещения эксплуатационного персонала об обнаруженных аномалиях, а развитые средства формирования отчетов и аналитики позволяют инженерному персоналу проводить всесторонний анализ технического состояния производственных активов.
Был ли вам полезен данный материал?

Подписывайтесь на канал ru-bezh.ru
в Яндекс.Дзен